Home About the Company Press and Media News TATRA PHOENIX with Euro 6 engines
TATRA PHOENIX with Euro 6 engines
27 February, 2015
The company TATRA TRUCKS a.s. introduces a technical, engineering and business news in the form of the heavy TATRA PHOENIX model range trucks with the engines meeting the most stringent Euro 6 emission specifications.
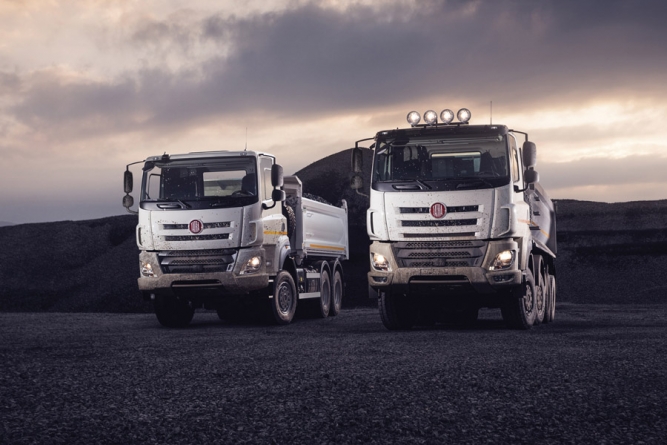
View fotogallery
Heavy trucks TATRA PHOENIX Euro 6 enrich the offering of the only Czech truck manufacturer exactly in accordance with the production strategy and in connection with the signing of the cooperation agreement with the Dutch truck manufacturer DAF TRUCKS N.V., the European part of the American automotive concern PACCAR.
The TATRA PHOENIX Euro 6 vehicles are directly based on the existing TATRA PHOENIX vehicle models with PACCAR engines of the previous emission specifications. Within the framework of mandatory requirements to comply with the strictest emission standards, collectively known under the acronym Euro 6, it brings a wide range of design enhancements increasing the operational efficiency to its operators and customers of TATRA TRUCKS a.s.
Since 2011, almost 500 vehicles of TATRA PHOENIX series in various modifications left the factory gate with the TATRA trademark on the hood, including vehicles specially adapted to the requirements of customers, representing a successful business connection between TATRA TRUCKS and international manufacturers and suppliers of certain components and assemblies. The TATRA PHOENIX model range, the main production schedule of the truck maker’s civil sector, is based on the highly successful TATRA chassis combination, the so-called "TATRA design concept", DAF cab, PACCAR engine, supplied also by DAF TRUCKS, and ZF or Allison gearboxes. For the Koprivnice motor works, customers, business partners, colleagues or brand admirers and supporters, TATRA PHOENIX means a significant, and especially most modern, platform within the concept of rigorous customer friendliness in the civilian production sector.
Tatra chassis concept
Unique Tatra chassis design concept comprises several proprietary technical solutions. The chassis with the central tube is unique in the world, originating in Tatra more than ninety years ago. Since then it has been tested under extreme conditions of all the world's continents. These vehicles successfully climb to almost all types of terrain on the planet.
The central tube and the frame welded to it by means of cross members form an extremely rigid vehicle suspension system, which is significantly stiffer in torsion and bending compared to a common frame design. An important fact is that the extreme chassis rigidity is the result of combining the central tube and frame. Long-term measurements and calculations show that the central tube significantly contributes to the torsional rigidity of the chassis.
High stiffness of the support structure decisively affects vehicle behavior and performance, as well as load to the frame and body. Flexural stiffness mainly affects the ride comfort, with theoretically less demands on the driver’s cab mounting. The torsional resistance affects the stability and steerability, thus providing high lateral stability when cornering on road surfaces with a transverse slope and rugged terrain. Proven to reduce stress on the welded frame and superstructure, such as tankers, cranes, etc., which allows for easier mounting of superstructures and mainly reduces the cost of maintenance and repair of such superstructures.
The Tatra concept chassis can work without a welded upper frame, which means that some of the superstructures can be attached by cross members directly to the central tube, which reduces material costs of the subframe for bodybuilders and allows for increased superstructure payload. A classical vehicle concept with a ladder frame can not afford similar solutions. The rigid chassis supporting structure, in conjunction with independently suspended swinging half-axles, allows for up to 30% higher off-road speed, in comparison to conventional vehicles, while maintaining comfort.
Optimizing TATRA PHOENIX Euro 6
The existing offer of the TATRA PHOENIX model range consists of a compact series of vehicles in 4x4, 6x6, 8x6 and 8x8 drive variants, supplemented with a 8x8 building machine with a total weight of 50 tons, or agricultural tractor units and other agricultural specials.
For the TATRA PHOENIX Euro 6 vehicle variants a number of design improvements have been prepared that have been rigorously tested for a long time on several vehicle prototypes as well as at the dynamic test-room or the assembly test-room at Kopřivnice.
The most obvious and fundamental structural change is the use of a new cab, whose base, as well as in the existing TATRA PHOENIX Euro 5 vehicles, is based on the DAF CF cab design, or the "construction" series respectively. The cab has completely been redesigned, especially in the floor section, including an extended front mounting on the frame. The bumper and the main headlight have received a new shape as well. The lower part of the bumper is made of steel and split into three parts to save the costs of possible replacement or repair. Even with the new cab and the transition to the Euro 6 engines, the approach angle remains to be 31 degrees as that of vehicles with Euro 5 engines. This is one of the best approach angle values for all-wheel drive trucks in the off-road segment.
Similarly to the vehicles with Euro 5 engines, a new bonnet with a unique appearance has also been designed for the new PHOENIX Euro 6 vehicles. The cab fender extensions have also been newly designed, with the turn signal indicator lights integrated. As with the Euro 5 variants, flexible mounting of the lower leg support in the cab was also applied in the new vehicles. Such a solution is time-proven in the toughest conditions. Cabs in two versions will also be installed on the new vehicles - a short one (day cab) and extended (sleeper cab). In order to extend the engine offering with another inline six-cylinder PACCAR MX-11 diesel engine, the cab position on the frame also changes, including associated bodywork parts.
New engines
A quite crucial change that, however, takes place "under the hood" is the extension of the engine offering and their emission specifications Euro 6. There are two types of PACCAR engines. The bigger MX-13 with a displacement of 13 l and the maximum power of 300 kW, 340 kW and 375 kW, and a "smaller" MX-11 with a displacement of 11 l and maximum power output of 271 kW, 292 kW and 320 kW. Unlike the emission variants Euro 3 and Euro 5, the PACCAR MX-13 engine was fundamentally redesigned. So, this is the first time when a Common Rail injection type engine is mounted in TATRA vehicles. Other engine design changes include in particular the integration of exhaust gas recirculation system and a new engine oil pan.
The PACCAR MX-11 engine is of a completely new design. To optimize the emission of harmful compounds in exhaust gases according to Euro 6 standards, both engines use a proven combination of exhaust gas recirculation system (EGR) and catalytic reduction (SCR), with which DAF TRUCKS as engine manufacturer has rich years of experience in the production for American brands Kenworth and Peterbilt that meet similar requirements under the North American legislation pursuant to EPA 10. The whole combination is complemented with a diesel particulate filter, called DPF. Within the implementation of the EGR system, the vehicle radiator was enlarged, as well as the intercooler, which has reflected in the design of a new vehicle frame, which expands to "Vee-shape" in the space behind the front axle forward.
The exhaust gas cleaning equipment in accordance with Euro 6 is spatially more demanding than the one meeting the previous standard. This also required a total reconfiguration of accessories mounted on the vehicle frame. Two basic combinations of exhaust tracts will be used for new models with Euro 6 engines. For 4x4 and 6x6 vehicles, it will be a "horizontal" version where the DPF and catalytic converter are arranged in a row in one block on the right side of the vehicle frame. The second option, normally used for 8x8 vehicles, features the "standing" design. The DPF filter is located on the frame right in the wheelbase of the first and second front axles, and the cylindrical catalyst is situated above it just behind the cab with the exhaust gas outlet oriented upward. The "standing" design can be mounted on a vehicle in 4x4 and 6x6 upon the customer’s request.
The whole system of the so-called "lab behind the muffler" is supplemented with a number of probes, sensors and additional functions, including for example, fuel injection for the DPF regeneration. The electronic air control system (EAC) complements the electronic system of the engine, the exhaust tract and other systems for the first time in the history of TATRA vehicles. The braking system is controlled by a new generation of EBS-3 anti-lock braking system from WABCO. Other electronic assistance systems are currently at the stage of final testing that will have an impact on even greater driving comfort and operational effectiveness.
Further design improvements relate to the front axle suspension. For vehicles with Euro 6 engines new dampers are used with a modified attenuation characteristics. The front torsion stabilizer and its mounting have undergone a major change. The mounting of the main steering lever with optimized geometry has also been revised and, in this connection, the front back-bone tube design has been modified as well.
Transmission options
As with the existing TATRA PHOENIX models with the Euro 5 engines, standard in-building of 16-speed ZF transmissions is used in the new trucks, both with manual transmission and automated shifting (AS-Tronic). Both variants can be complemented with intarders. Manual transmission is newly operated using bowdens, which significantly contributes to reducing the vibrations transmitted to the passenger compartment and thus to the driver’s work comfort. The automated gearshift system uses proprietary gearshift software jointly developed with ZF engineers.
The standard is to offer one-speed auxiliary transmission of TATRA’s proprietary design (in three gearing variants) and two-speed TATRA auxiliary transmission (in two gearing variants). The gear ratios of auxiliary transmissions are designed to contribute to the excellent fuel economy. The incorporation of fully automatic Allison transmissions is planned for the next year.
Customer friendliness
The TATRA PHOENIX Euro 6 vehicles will initially cover the same range of options as the previous model series. Additional versions will gradually emerge, optional equipment will be extended, as well as the development and expansion of after-sales services offered by this new model series. All with the priorities given by customer preferences, as always inherent to the helpful customer approach of TATRA TRUCKS a.s. However, a number of special solutions are currently being born in Kopřivnice to meet specific customer requirements, for which TATRA PHOENIX chassis will be used in the very near future.
History of TATRA-DAF cooperation
The TATRA and DAF truck makers have been working together since 2011, when TATRA PHOENIX model was launched, which won a significant award in a journalist poll Truck of the Year 2012 for the best all-wheel drive vehicle. TATRA manufactures the chassis, DAF supplies the cab, engine and transmission. The production and assembly of vehicles take place in the Koprivnice company. The cooperation of truckmakers includes from the beginning dealer network sharing and cooperation in the field of after-sale services.
The TATRA PHOENIX vehicles are sold to various sectors. Very positive references come, for example, from Lesy Slovenské republiky (Forests of the Slovak Republic), where a few dozens of timber forwarding sets operate, consisting of 6x6 TATRA PHOENIX tractor unit, or from other companies engaged in logging (e.g. Lesy CR, Kloboucká lesní. The TATRA PHOENIX vehicles also successfully replace the older Koprivnice models, as well as competing vehicles in quarries and surface mines, e.g. in the North Bohemian mines or Kaznejov kaolin plant belonging to LB-Minerals group. A number of construction companies use them as well. Thanks to the TATRA PHOENIX model in the agro tractor unit version, the TATRA trucks return also to the Czech and Slovak fields.